EXPERIMENTAL BLOOMERY IRONMAKING
in the Weald of Southern England in the 21st Century
PREPARATION OF THE ORE
The ore, preferably weathered to make it more friable, is washed to remove clay, broken with hammers to pieces up to 50mm in size and roasted in a fire to drive off moisture and convert the carbonates to their oxides and carbon dioxide. Roasting takes place in a shallow pit in which a fire is first lit and then more layers of wood laid on the embers before adding the ore. Another layer of wood is placed on top of the ore and the whole covered with corrugated iron sheets as the ore pieces sometimes explode, particularly if large, under the pressure of the steam and CO2 being driven off. After 24 hours the ore is cool enough to be collected and is stored in metal bins ready for crushing to about 10mm diameter which is a suitable size for smelting.
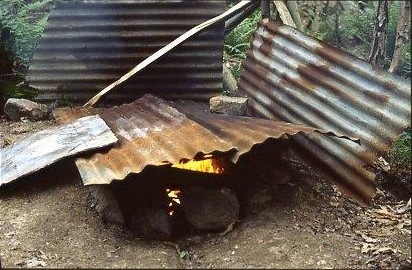 Image 4: Roasting the ore converts carbonates to oxides and increases porosity, making the ore easier to smelt.
An analysis of the chemical constituents of the ore as mined and after roasting is given in Table 1. Although the ore varies in hardness, its chemical composition is much the same. Sometimes, bivalve shells can be seen embedded in the ore indicating a source of the calcium carbonate.
Table 1 Analysis of Sharpthorne ore (weight %)
|
ROASTED |
UNROASTED (Hard) |
UNROASTED (Softer) |
FeO |
- |
46.88 |
46.03 |
Fe2O3 |
55.34 |
N/A |
N/A |
SiO2 |
9.34 |
6.75 |
8.30 |
CaO |
4.47 |
3.72 |
3.89 |
Al2O3 |
4.15 |
3.42 |
3.85 |
MgO |
2.27 |
2.02 |
2.08 |
Mn3O4 |
1.71 |
1.53 |
1.40 |
P2O5 |
0.47 |
0.46 |
0.44 |
Na2O |
0.11 |
0.08 |
0.11 |
TiO2 |
0.21 |
0.15 |
0.19 |
CO2(A) |
21.9 |
34.99 |
33.71 |
Fe(B) |
38.74 |
36.09 |
35.44 |
(Traces <0.05% V, Ba, Zr, Zn, Sr)
Notes: (A) CO2 by difference. (B) Fe available in oxide |
The analysis in Table 1 is by X-ray fluorescence, which does not record the amount of CO2 present from the carbonates, hence this is estimated from the balance remaining after those elements that can be measured have been determined. For a more detailed description of the estimates made click HERE.
The main minerals present are identified by X-Ray diffraction in Table 2. This technique is capable of identifying all the minerals present, including the carbonates.
Table 2 Minerals present in ore
Mineral |
Formula |
ROASTED |
UNROASTED (Hard) |
UNROASTED (Soft) |
Siderite |
FeCO3 |
Major |
Major |
Major |
Maghemite |
Fe2O3 |
Major |
None |
None |
Haematite |
Fe2O3 |
Trace |
None |
None |
Quartz |
SiO2 |
Minor |
Minor |
Minor |
Kaolinite |
Al2Si2O5(OH)4 |
Trace |
Trace |
Trace |
Calcite |
CaCO3 |
Trace |
Trace |
Trace |
After roasting, the colour of the ore changes from grey to red or sometimes maroon, and it becomes magnetic. The magnetic properties come from the mineral Maghemite the 'gamma' form of ferric oxide (Fe2O3). The roasted ore's porosity makes it much easier to break into particles of about 10mm diameter for smelting and also improves the rate of reduction since it is more permeable to gases.
Not all of the iron carbonate is converted to iron oxide in a single roast, but sufficient is converted to make it much easier to break the ore for smelting. Any carbonate remaining in the roasted ore decomposes in the upper section of the bloomery furnace as the temperature of the ore increases the further down the furnace shaft it descends. Too much carbonate remaining in the ore will cause the temperature to drop in the furnace as it absorbs heat when decomposing.
Continue to: The FURNACE
© Wealden Iron Research Group 2003
|