EXPERIMENTAL BLOOMERY IRONMAKING
in the Weald of Southern England in the 21st Century
The ORE
Iron ore in the Weald occurs largely as iron carbonate associated with the clay deposits. It forms buff- to grey-coloured bun-shaped nodules and masses, typically measuring between 5cm and 25cm in diameter, and also as tabular deposits up to 25cm thick, where it occurs as strata within the clays, silts and fine-grained sandstone.
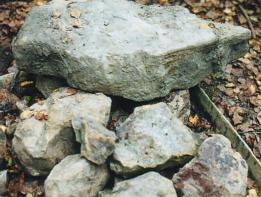 Image 1: Siderite iron ore as mined
For the WIRG experimental smelts, ore is usually collected from a present day quarry extracting clay for brick making at Sharpthorne in West Sussex. In places, the quarry face has shown sectioned 12 - 13th century mine pits, (dated by Carbon-14) and unmined ore, which we collect.
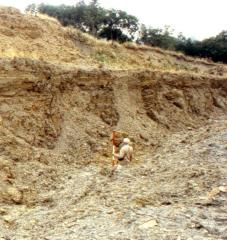 Image 2: Sectioned 12-13th Century ore pits at Sharpthorne, W. Sussex.
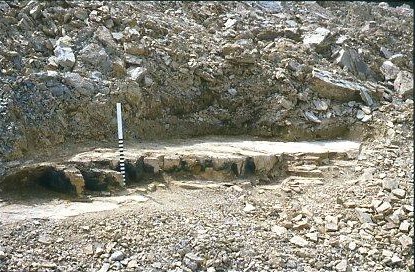 Image 3: Layers of ore at Sharpthorne.
The analysis of the ore we use in most smelts shows that it typically contains about 70% of the iron bearing mineral, Siderite, which is iron carbonate (FeCO3). It also contains about 7-9% silica (SiO2), which is important in the formation of a slag to remove the other non-iron bearing constituents such as alumina (Al2O3), calcium oxide (lime CaO) and magnesia (MgO). Ores from other parts of the Weald may contain varying amounts of these minerals. In particular, the amount of silica varies. If the silica content is too high, this will prevent a bloom being produced even when the iron content of the ore would be sufficient. In one trial we conducted using an ore containing around 30% silica, no bloom was produced, only prills of iron trapped in a viscous slag. This suggests the need to produce a fluid slag through which the prills of iron can pass and agglomerate to form the bloom.
Continue to: PREPARATION of the ORE
© Wealden Iron Research Group 2003
|