EXPERIMENTAL BLOOMERY IRONMAKING
in the Weald of Southern England in the 21st Century
The FURNACE
Smelting takes place in a cylindrical shaft furnace built of local Ashdown Sand. This contains about 88% silica, with sufficient clay naturally within it to bind the silica particles together. No stones or sticks were used in its construction, and the puddled 'sandy clay' was compacted between inner and outer metal cylindrical formers to shape the furnace walls. The furnace is about one metre high and 83cm outer diameter. The walls are 26cm thick, providing insulation to help retain the heat, and the inner diameter is 30cm giving a hearth area of about 700cm2.This design - but not the mode of construction - is believed to be similar to furnaces of the Roman period.
A slag-tapping arch at the bottom of the furnace allows slag, the molten waste material produced during smelting, to be removed at intervals during the smelt, provided it is sufficiently fluid to flow. The tapping arch is kept closed with turf at other times.
Air is forced into the furnace using two pairs of bellows worked alternately to provide a constant stream of air which creates a high temperature in the furnace in front of the tuyere. The temperature reached is above the melting point of the slag, but below that of the iron. A flexible hose, to accommodate movement of the bellows during pumping, and keep the pumpers far enough from the furnace to avoid inhaling toxic CO, is used to connect the bellows to the tuyere (pipe). The internal diameter of the tuyere is about 25mm and it passes through the furnace wall about 16cm above its base. For best results when tapping the slag, the tuyere is inclined downwards to keep the bottom of the furnace hot and to reduce the occurrence of slag running up the tuyere and blocking it. Inclinations of 15 to 30 degrees have proved suitable.
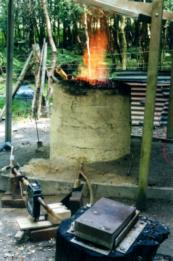
Image 5: The experimental bloomery furnace
The blowing rate is monitored and rates between 120 to 300 litres per minute (0.17 - 0.43 litres/min/cm2 of hearth area) have proved successful in producing blooms.
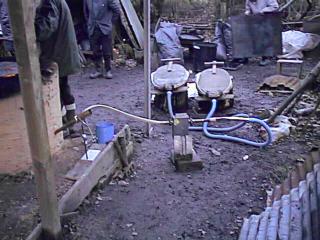
Image 6: The bellows are connected to the tuyere via the air gauge
The temperature of the furnace is monitored at two points by means of thermocouples. One is located 16cm and the other 38cm, from the top, placing the lower one about midway between the tuyere and the furnace top. Attempts to place thermocouples closer to the tuyere have resulted in their premature failure due to slag damage. Each 'K'-type thermocouple is protected by a metal sheath penetrating the furnace wall at 90 degrees to the tuyere and protruding to about the centre line of the furnace shaft.
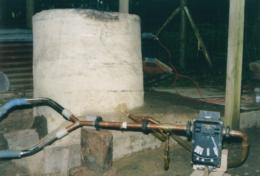
Image 7: Two thermocouples (right) are used to monitor shaft temperature and an air gauge for the blowing rate
Before a smelt, the furnace is preheated overnight with burning wood. Next morning, more wood is added and allowed to burn through to embers. During this preheat, the slag arch is partly open and serves as a damper to control the air drawn into the fire. To bring the furnace up to smelting temperature, the slag tapping arch is closed and the furnace filled with coarse charcoal and air applied from the bellows at a rate of about twice the normal smelting rate. More charcoal is added to keep the furnace full, and the carbon monoxide exiting the top of the furnace is ignited to prevent the escape of this toxic gas. When the temperature at the top thermocouple reaches about 750-800°C the conditions are suitable to add a mixture of ore and charcoal.
Continue to: The SMELT
© Wealden Iron Research Group 2003
|