EXPERIMENTAL BLOOMERY IRONMAKING
in the Weald of Southern England in the 21st Century
The BLOOM
When the furnace is nearly empty of charcoal, the bloom of iron may be seen adhering to the furnace wall just below the tuyere. The furnace is raked clear of any remaining charcoal through the tapping arch and the bloom broken away from the furnace wall by means of a crow bar. In recent experiments, we have partly consolidated the hot bloom inside the furnace using a heavy wooden pole.
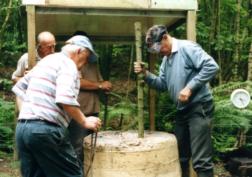 Image 10: Consolidating the bloom in the furnace prior to removal
At other times, we consolidate the bloom outside the furnace by reheating it in a separate hearth and hammering it, first with a wooden mallet on a wooden anvil to reducing the chilling effect, and finally with a heavy club hammer on a steel anvil to consolidate the bloom by expelling any trapped slag which has not run out during reheating and pressure weld individual particles of iron within the bloom.
Sometimes, we let the bloom cool so that we can weigh and section it to examine how dense it is.
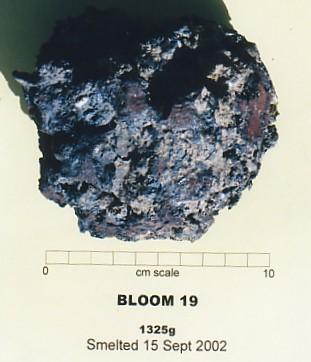 Image 11: The bloom - the yield is typically a quarter of the iron available in the ore
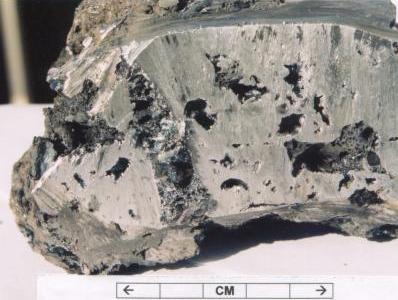 Image 12: A sectioned bloom after partial consolidation in the furnace
Generally, from 15kg of ore we produce a bloom weighing 1.5kg, ie a 10% yield from the ore. However, if we calculate the yield in terms of available iron, since the roasted ore contains only about 55% iron oxide (see Table 1) and the iron in the oxide Fe2O3 accounts for 70% of the weight of the oxide, (as some of the weight is oxygen) the available iron is 15 x 0.55 x 0.70 = 5.77kg equating to a yield of about 26%.
By looking at the microstructure of the bloom, and also the shape of the sparks it forms when touched on a grinding wheel, we can estimate the carbon content of small regions of the bloom. Often, this is quite high in some parts, with carbon contents as high as 0.8% occasionally observed at the surface and internal C values from zero to 0.5%. The carbon is present as iron carbide which forms as an intimate mixture of layers of iron carbide and ferrite known as pearlite. Carbon contents above about 0.3% are typical of a steel used for engineering applications, and can be hardened by quenching from a temperature of about 850°C (the temperature depends on the Carbon content). The areas of the bloom with almost zero carbon content are much softer and easier to forge into artefacts.
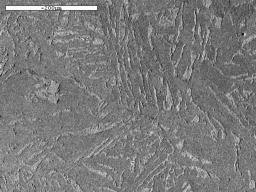 Image 13: Microstructure of a polished and etched section of bloom showing islands of pearlite
Continue to: COMPARISONS with Ancient Slags
© Wealden Iron Research Group 2003
|